Blog
How to Get Total Awareness and Control Over Inventory and High-Value Assets
Tracking high-value assets, returnable equipment, fleet maintenance, and consumable orders is a time-intensive task that can place major demands on personnel and chip away at budgets.
The alternative, on the other hand, is certainly worse: lack of awareness about equipment readiness or the whereabouts of critical assets, shortages of in-demand consumables like PPE, and even losses due to shrinkage.
Part of the problem many departments experience is a lack of standardized, comprehensive tools for asset tracking, recordkeeping, and accountability. Disparate systems for various assets means disjointed recordkeeping and no standardization. Hand logs and spreadsheets can cause redundancies and inaccuracies. A lack of visibility and awareness can create an environment that inadvertently encourages shrinkage.
Maybe worst of all, when critical scheduled maintenance or inspections are missed, out-of-service equipment can interfere with a department’s ability to serve.
But when your entire operation can rely on a single source of truth that’s both exhaustive in reach and item-level granular, you can achieve comprehensive, shared awareness and total control over inventory, maintenance, regulatory compliance, and even order scheduling for consumables.
Automated solutions can streamline and simplify every aspect of inventory and asset management — that is, if they include the right tools and structures to make it easy for everyone across the agency to access, use, and update these critical records.
Move Beyond Spreadsheets and Hand Logs
Sure, hand logs may seem easy to use, but they can be cumbersome, hard to track, and easy to ignore, too. Documents like spreadsheets can be hard to control and not always easy to access and use.
The shared visibility, standardized reporting, and auto-generated access logs that a solution like Omnigo Asset Management creates, on the other hand, offer department-wide awareness of more than item status. It’s easy to see who has control or custody of an item, when items were checked out or returned, and to whom specialty equipment or tools have been assigned.
But total inventory and asset management means an even broader — and deeper — awareness is possible, including:
- Custom inventory checklists specific to individual fleet vehicles or machinery
- Acknowledgements, including electronic signatures, added to equipment checkout procedures
- Periodic alerts for time-based preventive maintenance, warranty expirations, material replacements, or inspections
- Simple query-based reports to monitor use and review records
- Easy updates away from the desktop with barcode scanning and a mobile app
Omnigo Asset Management makes it easy to create instant records of inspections and inventory, and it’s just as simple to pull inventory records on demand to locate any item. Custom checklists can be created and added to inventory, inspection, calibration, or any other task.
Users can connect wirelessly using a mobile device to access the same records using the simplified app interface, and easily upload and attach digital files to records. Integrated barcode scanning enables item-level control and awareness, and paperless records reduce costs, improve efficiency, and save time.
Achieve Comprehensive, Granular Awareness of Materials & Assets
Improved visibility and awareness of the true costs associated with assets, inventory, maintenance and inspections, warranties and expirations, and usage of consumables can benefit any organization or operation.
In addition to public safety and law enforcement, organizations including hospitality, gaming, universities, laboratory or scientific operations, and nearly any other complex operation can benefit by reducing waste and ensuring operational safety, timely equipment calibration, and individual employee accountability.
Item-level awareness can be especially important for monitoring usage of consumables like PPE, maintenance supplies, or even materials that face seasonal demand. Keeping a close eye on consumable commodities can simplify reordering, prevent outages, and improve overall awareness of costs.
In terms of durable equipment and high-value assets, item-level monitoring can help improve awareness of wear and tear, maintenance and repair issues, and even an understanding of quality differences and brand preferences for certain tools or equipment. When usage and historical reports are easy to pull and understand, it’s easy to see which items are checked out and used more frequently than others and inform future purchasing decisions.
Customization and Implementation Should Be Simple, Too
Even the most advanced capabilities can only be effective if they’re easy to customize, implement, and use.
Your solution provider should be ready to help you configure, set up, and train users so your department can get started immediately and confidently. Expect intuitive user interfaces that require minimal training, and responsive customer service to help troubleshoot.
Ultimately, your inventory and asset management solution should make everyone’s job simpler and safer, while increasing visibility and accountability across your organization. Get a clearer vision of what item-level awareness and total inventory control can mean to your organization when you reach out and request a demo of Omnigo Asset Management.
More from the blog
View All Posts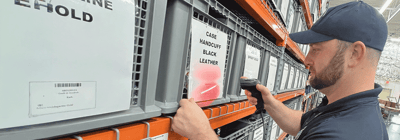
Pitfalls of Spreadsheets in Police Department Quartermaster Asset Management
Read More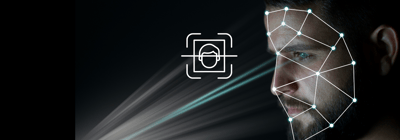
Enhancing Casino Security: The Advantages of Integrating Facial Recognition with Records Management Systems
Read More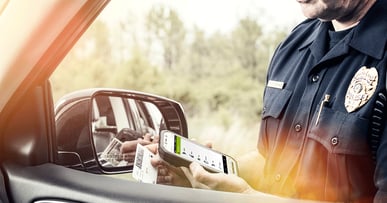
Don’t be left short-handed
Read MoreSubscribe to email updates
Stay up-to-date on what's happening at this blog and get additional content about the benefits of subscribing.